Did you make that yourself G? Certainly looks like theres a bunch of custom parts in there if not.
We've got a bfb one in our office, similar but the table just moves up and down and the heads move about in the 2 other planes like a router, i think it helps with building taller parts, stops them falling over. Amazing machine, considering it cost about 800 quid or something + 2 days of assembly by 'a competent engineer'*, ours has run probably 12hrs a day since we got it in feb.
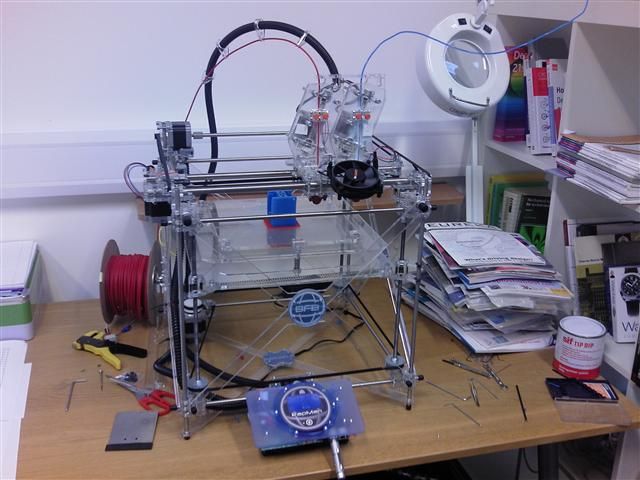
*took me 2 weeks before it was running, fuckers.
Built it from a kit £400. It's a Longboat Prussa. Supposed to take a couple of days to assemble and calibrate but took me more like a month, the physical assembly was easy enough but the instructions get patchy when it comes to the electronics and software etc. The kit came with bits missing and a couple of serious errors in the hot end which caused it to self destruct after about 2 hours of use... got it all tuned up now and starting to get decent prints.
Never had any parts fall over but I print on a heated glass bed (which is definitely the way to go).
There isnt a lot you can print that is strong enough to use as an actual item. I printed a super thick bashguard ring for my MTB which is holding up OK so far, and a case for some batteries, but mostly I just print mock ups of prototype parts which is enough to get a feel for the shape etc... It is very useful to be able to print out a pedal body say and put your foot on it and feel the pins etc then make modifications and print off another version within hours..
Cool thing is that I can now print out parts for upgrading the 3D printer, added a fan since this photo (which helps a lot with print quality).

G.